探密一汽大众工厂 解析速腾生产全过程
速腾作为大众PQ35平台的全新一代A级车,自05年年底投产一汽大众并于06年4月上市后深受众多消费者喜爱。日前,笔者受一汽大众邀请参观了国产速腾诞生地-一汽大众二厂。通过以下的详实解析,让我们一同体验速腾到底具备怎样的安全性以及领先制造工艺。
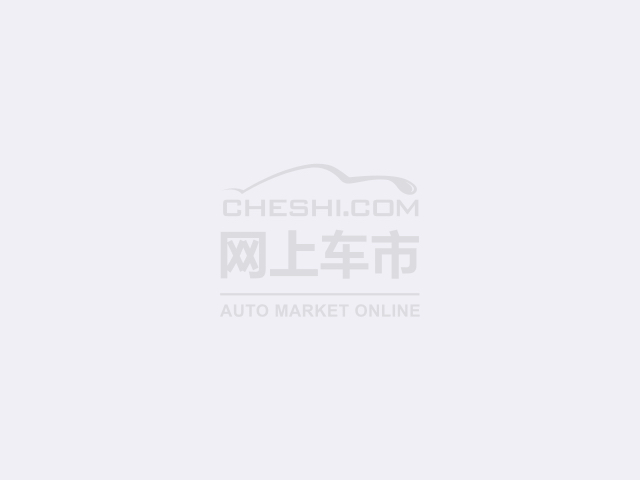
速腾产地一汽大众二厂毗邻一汽大众一厂,共同坐落在长春的一汽汽车生产基地。其中,一汽大众二厂共线生产迈腾、速腾和新宝来;一汽大众一厂则共线生产奥迪A6L、新A4L和捷达等车型。速腾等大众车型的整车制造流程主要分为冲压-焊接-涂装和总装四个环节,而焊接和总装又是最重要的两个环节。
一、焊接
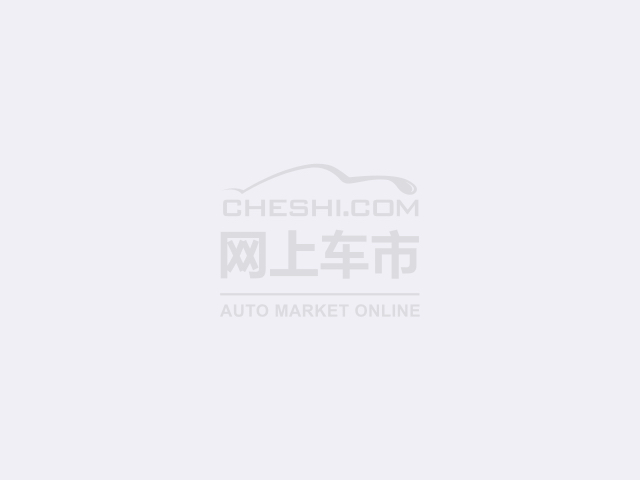
在焊装车间入口解剖车身介绍中,由热成型钢板技术制成的超高强度钢板车身,提升了速腾在同级别车型中的安全性能。速腾解剖车中彩色部分均为高强度热成型钢板,其中颜色越深代表强度越高。
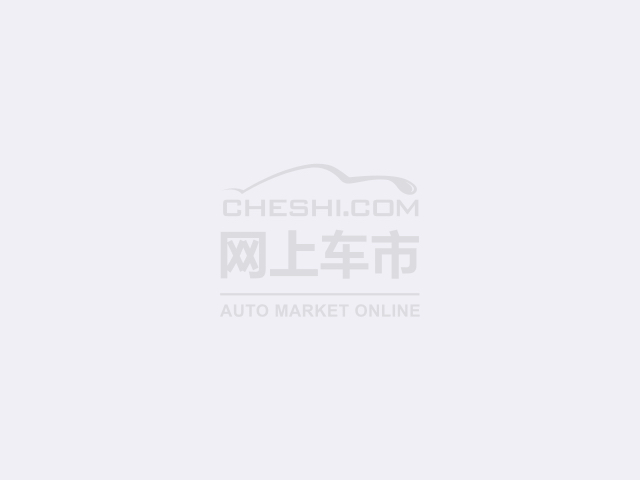
速腾总体激光焊接长度达33.2米,而顶盖处最长的1.6米激光焊缝在激光焊接程序中一次成型,使得速腾即使在剧烈碰撞时也只是小变形而不断裂,大大提高了车身的刚度和碰撞安全性。
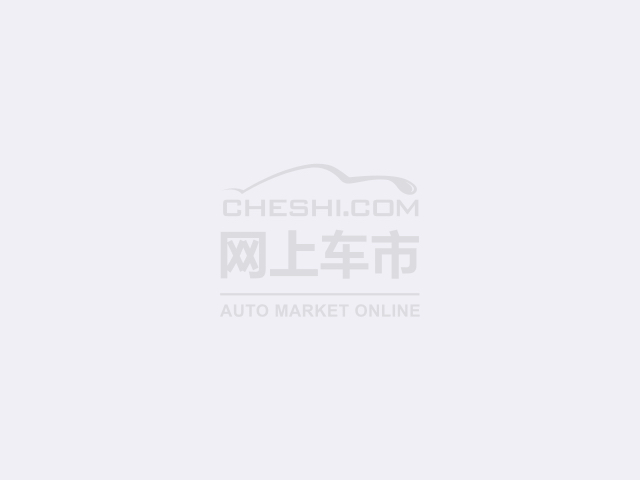
速腾在整个焊接过程中大量采用机器人和机械手臂,高效率机器人的运用可达到0.1毫米的重复定位精度,为车身加工质量的稳定提供了基础的保障,此外也进一步提升了生产效率。
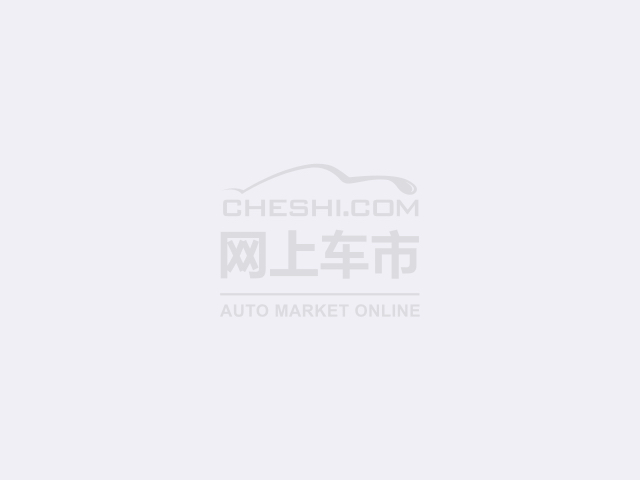
值得一提的是,在速腾等一汽大众生产线上均采用了AUDIT质量控制体系。AUDIT质量控制体系的核心理念是“站在用户的立场上,用比用户更挑剔的眼光对产品质量进行苛刻的评审检查”,质保部门最专业的检查人员对车辆的每一个细节进行检查并记录,然后开会集中对各项负责人进行讲评,负责人对相关的质量问题进行分析以及落实解决措施。